Jaw crushers are useful for crushing a variety of materials. They can be operated easily and are durable. However, the size of the feed opening and particle size capacity of a jaw crusher depend on the size of the jaw plates. A typical jaw crusher can process 70-80% of its feed opening, but this may vary from manufacturer to manufacturer. Moreover, the material used for the jaws can be a variety of materials, enabling it to be customized for the hardness and toughness of samples.
Single toggle jaw crusher

Single toggle jaw crushers have advantages over other types of jaw crushers because of their mechanism. In a single toggle jaw crusher, the crushing action is accomplished by transferring force between two opposed moving jaws that are coupled together. The maximum force transmission ratio is at the end of the active crushing stroke, while the minimum force transmission ratio is at the midpoint. The characteristics of the different mechanisms are listed in Table 4.
The high force transmission ratio is especially advantageous for crushing brittle materials. Such materials tend to fracture without deformation, and a single toggle jaw crusher would crush the material immediately. Its compact and simple structure also makes it less likely to damage a jaw. Furthermore, the movable jaw will move only a small distance, preventing excessive breaking. This makes it an efficient machine for crushing brittle materials. The advantages of single toggle jaw crushers include:
Easy to Operate
If you need to crush rocks and stones into smaller pieces, an easy to operate jaw crusher will do the job for you. Its crushing ratio is usually six to eight. Once crushed, the material is reduced to a size that can be fed into the next stage of the process, such as an impactor or cone crusher. Jaw crushers are used for many different kinds of materials including natural stone, rock, ore, and recycled concrete with a lot of rebar. The jaw ties on these crushers are very durable, and cheek plates can be changed easily.
Jaw crushers use pressure crushing as their main mechanism. The rock enters the jaw crusher and falls into the pit formed between the fixed crushing jaw and the moving jaw. The moving jaw follows the rock down the crusher’s chamber, crushing it until the particle is smaller than the predetermined size. The time it takes to crush a particle is an important determining factor in the crusher’s capacity. Frequency of opening and closing the jaws will determine how quickly or slowly a particle will be crushed, Sneak a peek at this website.
Durable
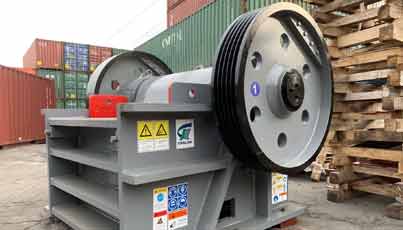
Choosing a durable jaw crusher is a crucial step in the process of making high-quality rock and concrete. A jaw crusher can produce consistent particle sizes and is easy to maintain. However, unlike other types of crushers, jaws are not as effective at reducing tough, ductile, and soft materials. Additionally, the final particle size range is less tightly controlled than that of other types of crushers. Therefore, if you are looking for a durable jaw crusher, you should consider its size and performance.
A durable jaw crusher is designed with deep crushing chambers, which maximise capacity, reduction ratio, and feed size. This design allows for large rocks to fall directly into the active portion of the crushing chamber. It also features an optimized nip angle, which ensures that material moves smoothly down the crushing chamber. These features increase productivity and optimise the use of jaw plates, and reduce the operational cost per ton. This is an excellent combination for a rock crushing application.